Steel Manufacturing
Overview
The steel industry involves the production of steel, a strong and durable metal alloy made primarily of iron, carbon, and other elements. The industry includes the extraction of iron ore, production of raw steel using blast furnaces, casting and rolling of the steel into various products, and the manufacturing of finished steel products such as structural components, appliances, and equipment.
The steel industry is a significant contributor to the global economy, providing employment and playing an important role in the development of infrastructure, transportation, and construction industries.
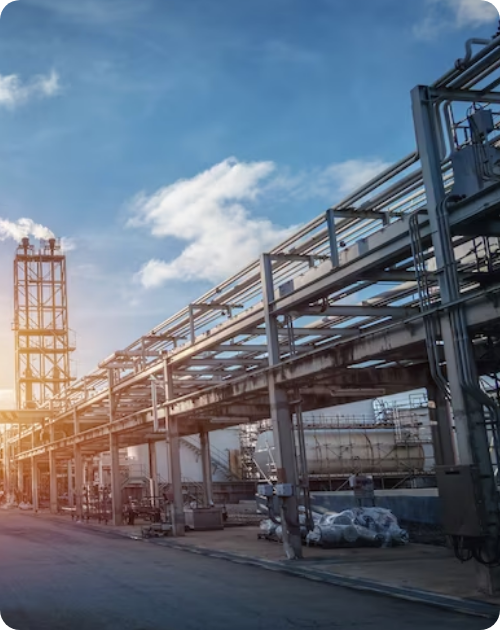
Design for the Future of Steel Manufactuting
Designing for the future of the steel industry using engineering simulations is a complex and multi-disciplinary task that involves the use of various simulation tools and techniques. Here are some key areas where DV Research uses engineering simulations which can play a critical role in shaping the future of the steel industry

Process optimization: Simulations are used to optimize various steel production processes, such as melting, casting, and rolling, to improve efficiency, reduce energy consumption, and enhance product quality.
New product development: Simulations are used to support the design and development of new steel products, such as high-strength steels and advanced high-strength steels, by predicting their mechanical properties and behavior under various loading conditions.
Process automation and control: Simulations are used to design and develop advanced control systems for steel production processes, allowing for improved process stability, reduced energy consumption, and increased production efficiency.
Sustainable steel production: Simulations are used to support the development of sustainable steel production processes, by predicting the environmental impact of different production scenarios and identifying opportunities for reducing greenhouse gas emissions and waste.
CFD Applications in Steel Industry
Computational Fluid Dynamics (CFD) is a simulation-based engineering tool used to analyze and predict the behavior of fluid flow and heat transfer. CFD works by solving mathematical equations that describe fluid behavior, based on physical principles such as continuity, momentum, and energy conservation.
CFD is widely used in the steel industry for process optimization, cooling and heating system design, fluid-structure interaction, and digital twinning. CFD is used to optimize steelmaking processes by predicting and optimizing fluid flow, heat transfer, and other physical phenomena. In cooling and heating system design, CFD is used to predict the performance of cooling and heating systems and optimize their design. In fluid-structure interaction, CFD is used to model the interaction between fluids and structures, such as pipelines and tanks. In digital twinning, CFD is used to create digital representations of physical systems, which is used for simulation, optimization, and control.
Using CFD in the steel industry offers many benefits, such as improved efficiency, reduced energy consumption, enhanced quality, and increased safety. CFD allows to predict and optimize fluid flow and heat transfer, leading to improved efficiency and reduced energy consumption. CFD also allows to analyze the behavior of physical systems, leading to enhanced quality and increased safety.

DV Research focuses on
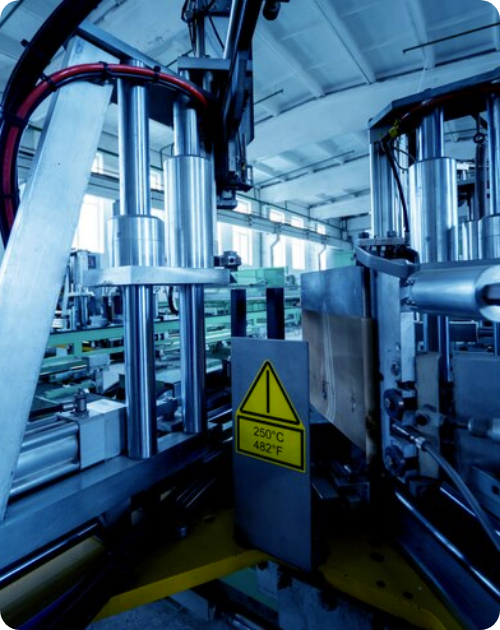
- Blast furnace burden distribution
- Combustion optimization in furnaces
- Predictive maintenance of furnaces
- Coal flow in coke ovens
- Iron ore discharge from ships
- Flow of sinter material
- Flow of coal in conveyor systems
- Liquid-liquid extraction in chemical processing
- Analysis of fluid flow and mixing in reaction vessels, pipelines and distillation columns
- Design of oil-water separation systems
- Flow and heat transfer in heat exchangers
- Combustion analysis in reheating furnaces
- Waste heat recovery
- Industrial burner design
- Design of vapor recovery systems
- NOx emissions control in boilers
FEA Applications in Steel Industry
Finite Element Analysis (FEA) is a computational method used for simulating and analyzing the behavior of complex systems and structures. The method is based on dividing the structure or system into smaller elements and then analyzing the interactions between these elements. FEA helps in understanding the behavior of a product or system under different loads and conditions, which is crucial in the design, optimization, and analysis of steel products.
FEA can perform a wide range of simulations, including structural, mechanical, thermal, fatigue, and fluid-structure interactions. Structural simulations help in determining the stability and strength of steel structures under different loads and conditions. Mechanical simulations are used to study the behavior of steel products under different types of mechanical loads, such as compression, tension, and torsion. Thermal simulations are used to understand the temperature distribution and thermal behavior of steel products. Fatigue analysis helps in determining the life cycle of a steel product under cyclic loading conditions.


Applications of FEA in the steel industry include structural design and optimization, material behavior analysis, welding and forging simulation, and fatigue analysis. FEA is used to optimize the design of steel structures and products, reducing the weight and increasing their strength. It is also used to analyze the behavior of materials under different conditions, including high temperature and pressure, which is crucial for the development of new steel products.
The benefits of using FEA in the steel industry include reduced weight, increased strength, improved reliability, and reduced costs. FEA helps in reducing the weight of steel products by optimizing their design, while maintaining or even increasing their strength. This leads to improved reliability and longer product life cycles. FEA also helps in reducing the costs of product development by providing a virtual testing environment, reducing the need for physical prototypes and testing.
DroneVionics focuses on
- Structural analysis
- Design optimization
- Fatigue analysis
- Welding simulation
- Residual stress analysis
- Corrosion analysis
- Fire resistance analysis
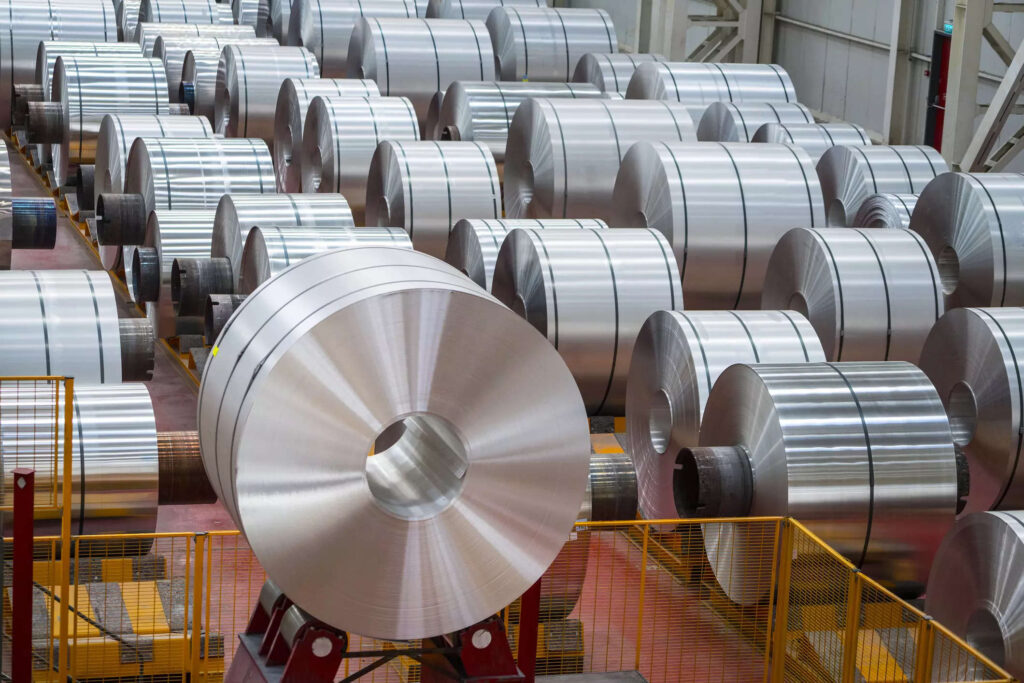