Turbomachinery
Overview
Turbomachinery deals with the design, construction, and operation of devices that generate mechanical power through the use of a fluid in motion. These devices, known as turbomachines, include turbines, pumps, compressors, blowers and fans.
Turbomachines work by using the energy of a moving fluid, such as water, air, or steam, to generate rotational motion. This rotational motion is then used to power various mechanical systems, such as generators, engines, and pumps.
DV Research has expertise in the fields of fluid dynamics, thermodynamics, and materials science, as well as the design and analysis of turbomachines tools and techniques. We also provide testing and optimization of turbomachines to ensure they operate efficiently and reliably.
Some common applications of turbomachinery engineering include power generation, aerospace, automotive, and industrial manufacturing.
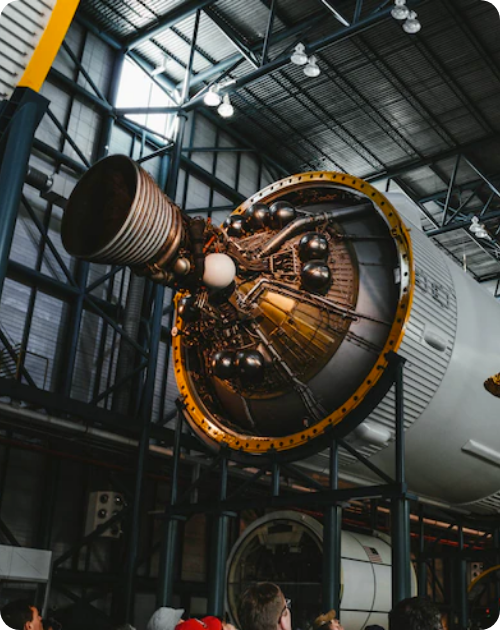

An official contract will be set based on your project description and details.

As we start your project, you will have access to our Portal to track its progress.

You will receive the project’s resource files after you confirm the final report.

Finally, you will receive a comprehensive training video and technical support.
Design for the Future of Turbomachinery
Turbomachinery is a broad field that encompasses the design, analysis, and testing of machines that use a rotating flow of gases or fluids to transfer energy. These machines, which include turbomachines like turbines, pumps, and compressors, are used in a variety of applications, including power generation, aircraft propulsion, and chemical processing. As such, the future of turbomachinery engineering will likely involve the development of more efficient and reliable designs that can meet the increasing demand for energy and support the transition to renewable energy sources.
One key area of focus in the future of turbomachinery engineering will likely be the design of machines that can operate at high-efficiency levels while also being able to withstand extreme operating conditions. This may involve the use of advanced materials and manufacturing techniques, as well as the development of new design approaches that can better handle the complex fluid dynamics involved in turbomachine operation.

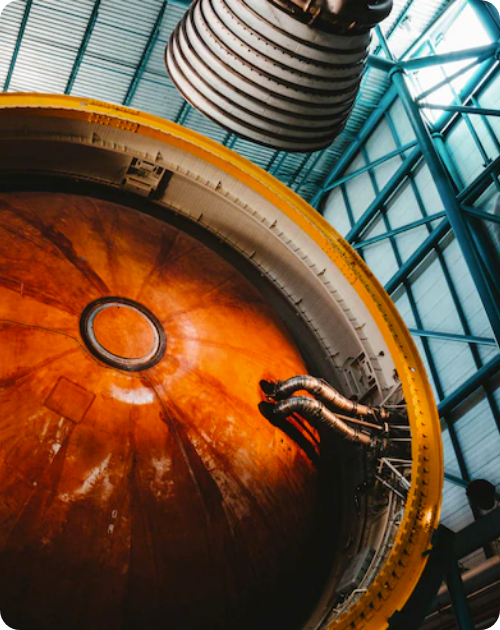
DV Research focuses on the development of designs and technologies that can support the transition to a more sustainable and efficient energy system, while also meeting the increasing demand for reliable and efficient energy production and processing.
Computer Aided Engineering (CAE)
in Turbomachinery
Simulation is a powerful tool that is widely used in turbomachinery engineering to design, analyze, and test the performance of turbomachines. By using computer models to simulate the flow of gases or fluids through a turbomachine, DV Research can predict the performance of the machine under various operating conditions and optimize its design for maximum efficiency and reliability.
There are a number of different simulation techniques that can be used in turbomachinery engineering, including computational fluid dynamics (CFD), which is used to simulate the flow of fluids through a machine, and finite element analysis (FEA), which is used to simulate the stresses and strains experienced by machine components.


Simulation is particularly useful in the early stages of turbomachine design whenever it requires to achieve the best design parameters and configurations for a given application. By running simulations with different designs and operating conditions, the DV Research team can quickly and efficiently identify the optimal design and operating parameters for a given machine.
Simulation is also an important tool for testing and evaluating the performance of prototype or production turbomachines. By comparing the simulated performance of a machine to its actual performance in testing, we can identify any discrepancies and make necessary adjustments to improve the machine’s performance.
Simulation plays a critical role in the design, analysis, and testing of turbomachines, and will likely continue to be an important tool in the field of turbomachinery engineering in the future.
Digitalization and data-driven
design in Turbomachinery
Digitalization and data-driven design are becoming increasingly important in the field of turbomachinery as they allow for more efficient and accurate design and optimization of these machines.
One way that digitalization is being used in the design of turbomachinery is through the use of computer-aided design (CAD) software. This software allows to create detailed 3D models of turbomachinery components and systems, which can be simulated and tested digitally before any physical prototypes are built. This can save time and resources by identifying and correcting design issues early in the development process.


Data-driven design involves the use of data analytics and machine learning techniques to optimize the design of turbomachinery. For example, data on the performance of existing turbomachinery can be used to identify trends and patterns that can inform the design of new machines. Data on the operational conditions of turbomachinery, such as temperature, pressure, and flow rates, can also be used to optimize the design of these machines for specific applications.
The use of digitalization and data-driven design in the field of turbomachinery is helping to improve the efficiency, reliability, and performance of these machines, which has important implications for a wide range of industries, including power generation, oil and gas production, and aerospace.