Chemical

An official contract will be set based on your project description and details.

As we start your project, you will have access to our Portal to track its progress.

You will receive the project’s resource files after you confirm the final report.

Finally, you will receive a comprehensive training video and technical support.
Design for the Future of Chemical Engineering
Chemical engineering deals with the design and operation of processes and systems for the production, transformation, and transport of chemical, energy, and material resources. As the world looks to address issues such as climate change, resource depletion, and environmental degradation, chemical engineering will play a critical role in developing sustainable solutions.
One key area of focus for the future of chemical engineering is the development of renewable energy sources. This could include designing processes for the production of biofuels, solar cells, and fuel cells, as well as developing new methods for storing and distributing energy.


This could include optimizing processes for the recycling of materials, such as plastics, metals, and paper, as well as developing new methods for extracting and using natural resources in a sustainable manner.
In addition to these areas, the future of chemical engineering will also involve the development of new materials and technologies for a wide range of applications, including medical devices, electronics, and construction materials.
DV Research involved in the development of innovative solutions that meet the needs of a rapidly changing world, while also protecting the environment and promoting sustainability.
Simulation in chemical engineering is the use of computer-based models to analyze and design chemical processes and systems. These simulations are used to predict the behavior of a chemical process under different operating conditions, optimize process design, and identify potential problems or bottlenecks.
DV Research focuses on:
Process simulation: This type of simulation is used to model and analyze the behavior of a chemical process, including the flow of materials, energy, and mass, as well as the chemical reactions that take place within the process.
Process control simulation: This type of simulation is used to design and optimize the control systems for a chemical process, including the selection of control variables, control algorithms, and control hardware.
Reaction engineering simulation: This type of simulation is used to model and analyze chemical reactions and the factors that influence them, including the kinetics of the reaction, the effect of temperature and pressure, and the role of catalysts.
Thermodynamics simulation: This type of simulation is used to predict the behavior of chemical systems under different thermodynamic conditions, including the prediction of phase equilibria, vapor-liquid equilibria, and chemical reaction equilibria.
Simulations are a powerful tool for chemical engineers, as it allows testing and optimizing process designs without the need for expensive and time-consuming physical experimentation. It helps to identify potential problems or bottlenecks in a process, allowing one to address these issues before they become major problems.

Process Simulation

DV Research uses computer software to model and analyze the behavior of industrial processes. It is a popular tool used in the chemical and process industries to design, optimize, and troubleshoot processes and equipment.
Process simulation involves creating a digital model of a process, which include the flow of materials, energy, and information through the process. The model is used to analyze the behavior of the process under different conditions and to predict the outcomes of changes to the process.
DV Research expertise excels in a wide range of applications, including the design of new processes, the optimization of existing processes, the analysis of process performance and efficiency, and the identification and troubleshooting of problems in a process.
Reaction Engineering
Reaction engineering deals with the design and optimization of chemical reactions. It involves the study of chemical kinetics, thermodynamics, and transport phenomena to understand and predict the behavior of chemical reactions and design appropriate reaction systems.
Reaction engineering simulation involves the use of computer software to model and simulate chemical reactions and predict the behavior of reaction systems. These simulations are used to optimize the design of chemical reactors, predict product yields and selectivity, and optimize the operating conditions of chemical processes.
DV Research works in a variety of applications of Reaction Engineering, including the design of chemical plants, the optimization of industrial chemical processes, and the development of new chemical products.
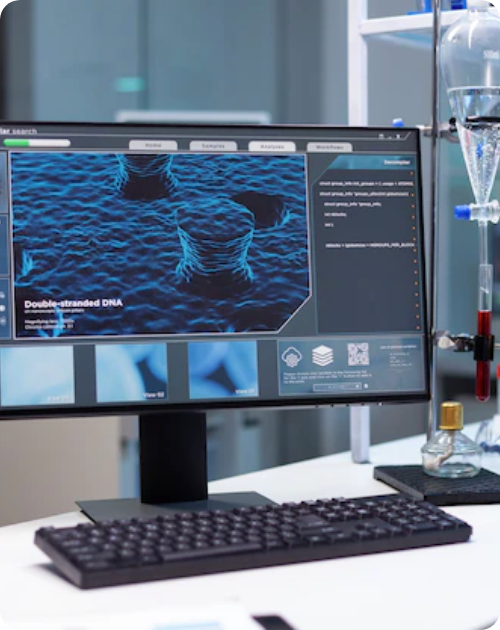